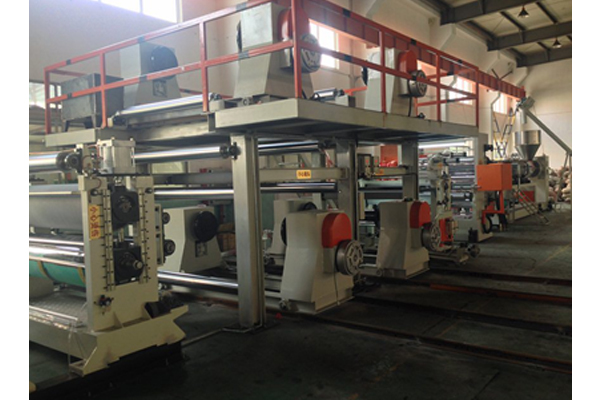 |
Lu: su composite panels based on plastic core material, the surface composite decorative coating of a kind of compound aluminum plate, its characteristic is colour diversity, light weight, easy to machining, strong weatherability, and many other advantages, so in the domestic and the world got a lot of use in many countries. The company production of aluminum-plastic composite board production line, advanced electromagnetic heating technology, over 40% of energy than conventional heating technology, achieve energy conservation and emissions reduction effect, greatly reduces the operating costs for the user, thus provides the market competitiveness. Production line mainly include extruder, three-roll calender machine, rolling machine, aluminum foil composite machine, shearing machine and other equipment The equipment parameters 1, raw material Low PE core material: LDPE, HDPE, high density polyethylene or PE reworked material Aluminum coil: width: 1000-1600 - mm Thickness: 0.02 0.5 mm Weight: 5000 kg/roll The largest diameter: Φ 1500 mm Drum diameter: 150 / Φ Φ 405 mm Polymer film: width: 1000-1600 mm Thickness: 0.02 0.05 mm Weight: 60-80 - kg/roll Protection film: width: 1000-1600 - mm Thickness: 0.03 0.08 mm Weight: 60-80 - kg/roll 2, finished product lu: su composite panels Width: 1000-1600 - mm Thickness: 1.5-6 mm (with the difference of 0.03 mm or less) Length: according to the production need to set 3, equipment speed: the maximum design speed is 7 m/min, 4, production capacity Produce 1220 mm * 2440 mm * 4 mm standard aluminum-plastic plate, with continuous production 24 hours a day, 300 days a year Production: 1158000 square meters Characteristics of the equipment 1, with large length to diameter ratio of mixed type efficient plasticizing exhaust type screw, equipped with water ring vacuum pump forced out plastic plasticizing process of gas, suitable for different quality of plastic processing, to ensure that the extrusion molding plastic core board surface no bubble, smooth and dense Fit for polymer film (film adhesive). 2, adopts hydraulic quick non-stop change filter head, guarantee to effectively filter the impurity in the plastic, non-stop fast in network, reduce labor intensity, ensure the continuity of plastic core board. 3, three roll mirror calender with high precision, good rigidity, can adjust the calender roll gap between precision, to ensure that the plastic core plate thickness tolerance, uniform cooling, board face level off is smooth. 4, USES multiple sets of mirror composite roller, aluminum coil, polymer film automatic tension control, adaptive composite aluminum coil thickness from 0.02 mm to 0.02 mm and high temperature, low temperature composite technology, can produce high quality more than 4 mm high quality of the cladding, 1 mm ~ 3 mm decoration inside the wall, 5, choose efficient electromagnetic heating technology, PID intelligent temperature control, ensure the plus or minus 2 ° roller surface temperature difference; Energy saving more than 40%, to achieve the safety and environmental requirements stipulated by the state. 6, using precision shearing machine, fast, smooth cutting board, the application of programmable controller PLC, an exact length, production quantity can be accumulated to store, the other optional photoelectric or servo. 7, all motor adopts high quality frequency speed regulator and programmable controller PLC control, easy to realize on-line growth and deceleration control, high degree of automation. |
|
|