Steel plate heat (electric galvanized) production line |
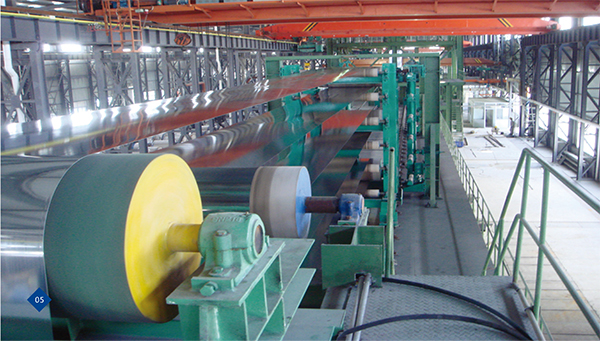 |
Steel plate hot galvanizing production line is in the steel coil with double high temperature hot dip plating a layer of zinc alloy plating equipment, production line consists of decoiler, welding machine, machine, degreasing cleaning unit, continuous annealing furnace, zinc pot, air knife, light machine, drawing machine, oil machine, shearing machine, winding machine and other equipment. Ⅰ.The parameters of the equipment: 1, material: cold-rolled carbon structural steel, quality carbon structural steel and low alloy steel 2, strip width: 600 ~ 1250 mm 3, the strip thickness: 0.15 ~ 3.5 mm : 4, coil diameter from 800 ~ 2000 mm 5, process speed: 80 ~ 200 m/min 6, the types of energy: electricity, natural gas, liquefied petroleum gas, gas, steam, air, compressed air, etc 7, state: ordinary zinc zinc flower, small flowers, finishing zinc, zinc flower 8, coating thickness: 50 ~ 300 g/m2 (double) 9, post-treatment of plating: light the whole affair, pull, fingerprint resistant coating/passivation, painting oil 10, continuous annealing furnace, horizontal/vertical/L Ⅱ.The characteristics of the equipment: 1, configuration, strip or efficient electrolytic cleaning chemical cleaning section, optional horizontal spray or vertical injection combined with cleaning mode, star and unique electrolytic cleaning ejector mixer technology, a higher current efficiency and avoid the board out of the trough the secondary oil contamination, directional overflow ensure electrolyte level surface rarely detonating gas bubble, use high security system. 2, no oxidation (NOF) and the combination of radiant tube heating (RTH) technology, fast heating, high thermal efficiency, double cross limit air-fuel ratio control method, a finer, special compound selection of refractory material, can significantly improve the insulation effect of high temperature and service life, international leading natural gas energy saving technology, greatly reduce the production cost. 3, annealing strip after reduction of cooling circulation use protective gas jet cooling, frequency control of motor speed control, adopts high speed jet method, strip cooling speed and uniform, can accurately control the strip into the process temperature of zinc pot. 4, setting machine, light machine, which can effectively improve the quality of the finished surface and flatness, improve product and cold punching machinery coating performance. 5, using flue gas waste heat recovery technology, through the heat exchange between flue gas and water or waste heat steam temperature of boiler flue gas waste heat and supply cleaning liquid heating, improves the heat energy utilization, the energy consumption of the product. 6, adopt spray ceramic induction heating zinc pot, heat fast, uniform temperature and the alloy components, long life and less zinc slag, furnace configuration in wet nose nitrogen and zinc circulating pump device can significantly improve the strip surface precision, especially suitable for electrical appliances coating substrate quality requirement. 7, the coating thickness measuring instrument can real-time monitor coating thickness of the actual, guide the accurate adjustment of air knife. 8, with rapid switching device of fingerprint resistant coating roller coater, which can effectively optimize the process of equipment layout, reduce building investment, at the same time in the strip surface can obtain accurate organic or compound coating 9, electric drive control system adopts vector frequency control of motor speed, dc bus power supply technology, greatly reduce the consumption of electrical energy. EPC and CPC deviation, field bus control technology, such as good man-machine interface, stable and reliable equipment. |
|
|